DIFERENCIA ENTRE PAVIEMTOS RÍGIDOS Y FLEXIBLES

En el pavimento rígido, el hormigón absorbe gran parte de los esfuerzos que se ejercen sobre el pavimento, mientras que en el pavimento flexible este esfuerzo es transmitido hacia las capas inferiores.
REQUERIMIENTOS MÍNIMOS PARA PAVIMENTOS HIDRÁULICOS.
Requisitos de los Materiales.
Dosificación.
Equipamiento Necesario.
Procedimiento Constructivo.
Juntas de Hormigonado.
Sellos de Juntas.
Curado y Protección del Pavimento de Hormigón.
Controles y Ensayos.
Recomendaciones.
Prevención y Corrección de Defectos.
REQUISITOS DE LOS MATERIALES DOSIS MÍNIMA DE CEMENTO
Grado corriente 320 kg / mt3 ·
Grado alta resistencia 280 kg / mt3
En todo caso, el cemento a ocupar será de grado alta resistencia y deberá cumplir con la Norma Chilena NCh 148.
AGUA DE AMASADO..
El agua de masado deberá ser limpia, exenta de sustancias perjudiciales y satisfacer los requisitos del Laboratorio Nacional de Vialidad nº 101 ( L.N.V., Chile ).
Límites mínimos tolerables de sustancias en el agua:
Turbidez: 1000 partes por millón. ·
Materiales orgánicos: 0,05 gramos por litro.
Acidez 6 a 8.
Cloruros 2 kg/m3.
Sulfatos 1 k/m3.
ARIDO GRUESO.
Comúnmente llamado grava, ripio o chancado.
Características:
El tamaño máximo absoluto será de 40 0 50 mm.
Desgaste según procedimiento de Los Angeles , máximo 35 % según método L.N.V. 75.
Porcentaje que pasa por el tamiz ASTM Nº 200, máximo 0.5 % en peso, según L.N.V. 70.
Porcentaje de partículas chancadas, mínimo 50 % en peso, según método L.N.V. 3.
Si este tamaño máximo aumenta, se puede disminuir la razón agua- cemento, reduciéndose el consumo de cemento. Sin embargo este tamaño máximo tiene un límite, en los pavimentos este límite tienen relación con el espesor de la losa.
ARIDO FINO.
Composición granulométrica según tabla nº 2 de la especificación L.N.V. 70.
Porcentaje que pasa por el tamiz ASTM Nº 200 , será máximo 2 % en peso según L.N.V. nº 70.
Para el agregado fino, es importante determinar su módulo de fineza, que se obtiene del análisis granulométrico. Este nos permite clasificar las arenas, para su uso en las mezclas, en gruesas, finas y semi-finas.
ADITIVOS.
Son sustancias que se emplean en pequeña cantidad, para modificar alguna de las propiedades del hormigón cuando esta fresco, o para proporcionar alguna condición especial después de endurecido.
Deberán cumplir con lo establecido en NCh 2182, y ser controlados según NCh 2281. (Normas Chilenas, del Instituto de Normalización Nacional de Chile).
Las propiedades que un aditivo puede modificar, mejorando las características del hormigón fresco, son:
Trabajabilidad (docilidad): Mediante aditivos Plastificantes.
Fraguado y Resistencia: Mediante aditivos Aceleradores o Retardadores; los aceleradores son apropiados para tiempo frío y en reparaciones; los retardadores en transporte, bombeo e inyección de mortero.
Retracción de fraguado: Mediante aditivos expansores
Las propiedades que un aditivo proporciona después de endurecido el hormigón, son:
Impermeabilidad: Mediante aditivos Hidrófugos
Durabilidad: Mediante aditivos dispersores, que tienen por objeto dispersar las partículas de cemento que por lo general se encuentran aglomerados localmente, produciendo una masa más homogénea y de mayor durabilidad.
DOSIFICACIÓN.
La dosificación del hormigón consistirá en combinar en proporciones definidas, los diferentes componentes, de modo de obtener un hormigón que cumpla con la resistencia, docilidad, durabilidad y restantes exigencias requeridas en el proyecto.
En todo caso, cualquier estudio de dosificación estará respaldado por ensayes que acrediten una resistencia característica a la flexotracción mínima de 4.6 MPA a los 90 días, u otra que especifique el proyecto, considerando una fracción defectuosa del 20 %.
Requerimientos básicos.
Cantidad mínima de cemento: 340 Kgs. de cemento por metro cúbico.
Asentamiento: Según INN Nch 1019 c72 entre 2 y 5 cms.
Resistencia: Nominal cúbica de 360 kgs./cm2 a los 90 días.
DOSIFICACIÓN PRÁCTICA.
Cemento de grado alta resistencia: 42.5 kilos.
Grava o ripio : 85 litros.
Arena humeda : 40 litros.
Agua aproximada : 15 litros.
Esta es una dosificación recomendada por Hormigones Premix, con un rendimiento de 111 litros. En todo caso, se recomienda su uso para obras de pequeña envergadura, requiriéndose un estudio más acabado en obras mayores.
EQUIPOS PARA LA COLOCACIÓN Y COMPACTACIÓN DEL HORMIGÓN.
REQUERIMIENTOS MÍNIMOS PARA PAVIMENTOS HIDRÁULICOS.
Requisitos de los Materiales.
Dosificación.
Equipamiento Necesario.
Procedimiento Constructivo.
Juntas de Hormigonado.
Sellos de Juntas.
Curado y Protección del Pavimento de Hormigón.
Controles y Ensayos.
Recomendaciones.
Prevención y Corrección de Defectos.
REQUISITOS DE LOS MATERIALES DOSIS MÍNIMA DE CEMENTO
Grado corriente 320 kg / mt3 ·
Grado alta resistencia 280 kg / mt3
En todo caso, el cemento a ocupar será de grado alta resistencia y deberá cumplir con la Norma Chilena NCh 148.
AGUA DE AMASADO..
El agua de masado deberá ser limpia, exenta de sustancias perjudiciales y satisfacer los requisitos del Laboratorio Nacional de Vialidad nº 101 ( L.N.V., Chile ).
Límites mínimos tolerables de sustancias en el agua:
Turbidez: 1000 partes por millón. ·
Materiales orgánicos: 0,05 gramos por litro.
Acidez 6 a 8.
Cloruros 2 kg/m3.
Sulfatos 1 k/m3.
ARIDO GRUESO.
Comúnmente llamado grava, ripio o chancado.
Características:
El tamaño máximo absoluto será de 40 0 50 mm.
Desgaste según procedimiento de Los Angeles , máximo 35 % según método L.N.V. 75.
Porcentaje que pasa por el tamiz ASTM Nº 200, máximo 0.5 % en peso, según L.N.V. 70.
Porcentaje de partículas chancadas, mínimo 50 % en peso, según método L.N.V. 3.
Si este tamaño máximo aumenta, se puede disminuir la razón agua- cemento, reduciéndose el consumo de cemento. Sin embargo este tamaño máximo tiene un límite, en los pavimentos este límite tienen relación con el espesor de la losa.
ARIDO FINO.
Composición granulométrica según tabla nº 2 de la especificación L.N.V. 70.
Porcentaje que pasa por el tamiz ASTM Nº 200 , será máximo 2 % en peso según L.N.V. nº 70.
Para el agregado fino, es importante determinar su módulo de fineza, que se obtiene del análisis granulométrico. Este nos permite clasificar las arenas, para su uso en las mezclas, en gruesas, finas y semi-finas.
ADITIVOS.
Son sustancias que se emplean en pequeña cantidad, para modificar alguna de las propiedades del hormigón cuando esta fresco, o para proporcionar alguna condición especial después de endurecido.
Deberán cumplir con lo establecido en NCh 2182, y ser controlados según NCh 2281. (Normas Chilenas, del Instituto de Normalización Nacional de Chile).
Las propiedades que un aditivo puede modificar, mejorando las características del hormigón fresco, son:
Trabajabilidad (docilidad): Mediante aditivos Plastificantes.
Fraguado y Resistencia: Mediante aditivos Aceleradores o Retardadores; los aceleradores son apropiados para tiempo frío y en reparaciones; los retardadores en transporte, bombeo e inyección de mortero.
Retracción de fraguado: Mediante aditivos expansores
Las propiedades que un aditivo proporciona después de endurecido el hormigón, son:
Impermeabilidad: Mediante aditivos Hidrófugos
Durabilidad: Mediante aditivos dispersores, que tienen por objeto dispersar las partículas de cemento que por lo general se encuentran aglomerados localmente, produciendo una masa más homogénea y de mayor durabilidad.
DOSIFICACIÓN.
La dosificación del hormigón consistirá en combinar en proporciones definidas, los diferentes componentes, de modo de obtener un hormigón que cumpla con la resistencia, docilidad, durabilidad y restantes exigencias requeridas en el proyecto.
En todo caso, cualquier estudio de dosificación estará respaldado por ensayes que acrediten una resistencia característica a la flexotracción mínima de 4.6 MPA a los 90 días, u otra que especifique el proyecto, considerando una fracción defectuosa del 20 %.
Requerimientos básicos.
Cantidad mínima de cemento: 340 Kgs. de cemento por metro cúbico.
Asentamiento: Según INN Nch 1019 c72 entre 2 y 5 cms.
Resistencia: Nominal cúbica de 360 kgs./cm2 a los 90 días.
DOSIFICACIÓN PRÁCTICA.
Cemento de grado alta resistencia: 42.5 kilos.
Grava o ripio : 85 litros.
Arena humeda : 40 litros.
Agua aproximada : 15 litros.
Esta es una dosificación recomendada por Hormigones Premix, con un rendimiento de 111 litros. En todo caso, se recomienda su uso para obras de pequeña envergadura, requiriéndose un estudio más acabado en obras mayores.
EQUIPOS PARA LA COLOCACIÓN Y COMPACTACIÓN DEL HORMIGÓN.
Moldes metálicos: Deben ser rectos, sin torceduras con resistencia lateral para soportar la presión del hormigón sin flexionarse y de altura igual al espesor del pavimento.
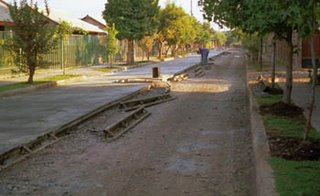
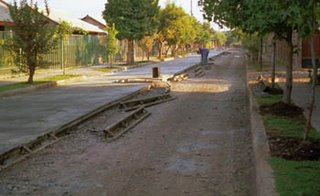
VIBRADORES EXTERNOS O DE SUPERFICIE:
Cercha vibradora: es una viga sencilla o doble, de largo suficiente para cubrir el ancho de la losa. Pueden estar provistas de excéntricas o de vibradores de encofrado de manera que la regla a medida que se desliza sobre la arista de los moldes o sobre rieles especiales transmita las vibraciones al hormigón.
Vibrador de bandeja: consiste en una bandeja horizontal (o serie de bandejas) que se extiende a todo el ancho de la losa, descansando completamente en ella sin tocar los moldes, se debe montar en un marco horizontal capaz de elevarlo fuera del contacto con el pavimento. Se emplea exclusivamente para compactar.
Alisadora de rodillos: enrasa la superficie al tiempo que consolida el hormigón debido a su acción de golpe y vibración. En general se efectúan dos pasadas, la 1ª para compactar (alta frecuencia) y la 2ª para dar el acabado (baja frecuencia). La docilidad del hormigón debe ser mayor a 5 cm.
Vibradores internos: se emplean como complemento de los equipos de superficie y en particular de las cerchas vibradoras.
Los equipos de alto rendimiento están provistos de 5 a 6 vibradores de inmersión montados en un marco, el cual debe tener movimiento vertical para poder sacar o introducir los vibradores.
Los trenes pavimentadores constan de un esparcidor de hormigón de gusano (sinfín) o paleta, que mantiene una alimentación en un espesor uniforme en todo el ancho de la faja. Lo sigue una batería de vibradores de inmersión los cuales producen la compactación en toda la masa a medida que la máquina avanza, seguido de una placa vibratoria que alisa la superficie.
HERRAMIENTAS PARA EL ACABADO SUPERFICIAL.
Platachos: están constituidos por una base de madera o metal de gran superficie provistos de un mango largo articulado.Cepillos, arpillera: para obtener la textura superficial rugosa, se utilizan cepillos anchos de cerda o nylon provistos de mangos o arpillera que se desliza transversal o longitudinalmente sobre la superficie.

Vibrador de bandeja: consiste en una bandeja horizontal (o serie de bandejas) que se extiende a todo el ancho de la losa, descansando completamente en ella sin tocar los moldes, se debe montar en un marco horizontal capaz de elevarlo fuera del contacto con el pavimento. Se emplea exclusivamente para compactar.
Alisadora de rodillos: enrasa la superficie al tiempo que consolida el hormigón debido a su acción de golpe y vibración. En general se efectúan dos pasadas, la 1ª para compactar (alta frecuencia) y la 2ª para dar el acabado (baja frecuencia). La docilidad del hormigón debe ser mayor a 5 cm.
Vibradores internos: se emplean como complemento de los equipos de superficie y en particular de las cerchas vibradoras.
Los equipos de alto rendimiento están provistos de 5 a 6 vibradores de inmersión montados en un marco, el cual debe tener movimiento vertical para poder sacar o introducir los vibradores.
Los trenes pavimentadores constan de un esparcidor de hormigón de gusano (sinfín) o paleta, que mantiene una alimentación en un espesor uniforme en todo el ancho de la faja. Lo sigue una batería de vibradores de inmersión los cuales producen la compactación en toda la masa a medida que la máquina avanza, seguido de una placa vibratoria que alisa la superficie.
HERRAMIENTAS PARA EL ACABADO SUPERFICIAL.
Platachos: están constituidos por una base de madera o metal de gran superficie provistos de un mango largo articulado.Cepillos, arpillera: para obtener la textura superficial rugosa, se utilizan cepillos anchos de cerda o nylon provistos de mangos o arpillera que se desliza transversal o longitudinalmente sobre la superficie.

PROCEDIMIENTO CONSTRUCTIVO.
Sobre la base compactada, la que deberá estar limpia y cuyas especificaciones están dadas en el capítulo correspondiente, se recomienda aplicar una membrana asfáltica del tipo MC-30 o similar, con el objetivo de crear un puente de adherencia entre la base y el hormigón fresco. Además, sirve para minimizar problemas de alabeo de losas y evitar la pérdida de agua de amasado.
Deberán verificarse los requisitos topográficos, ya sea de la base, como así mismo del trazado, pendientes y peraltes.
Se recomienda un cono de trabajo de entre 2 y 5 cms, para el caso de un hormigón vibrado, y entre 5 y 8, en el caso de hormigón apisonado.
Por otra parte, no se colocará hormigón con temperaturas superiores a 35 º C, ni con temperaturas inferiores a 5ºC. En caso contrario, deberán tomarse las precauciones necesarias.

Sobre la base compactada, la que deberá estar limpia y cuyas especificaciones están dadas en el capítulo correspondiente, se recomienda aplicar una membrana asfáltica del tipo MC-30 o similar, con el objetivo de crear un puente de adherencia entre la base y el hormigón fresco. Además, sirve para minimizar problemas de alabeo de losas y evitar la pérdida de agua de amasado.
Deberán verificarse los requisitos topográficos, ya sea de la base, como así mismo del trazado, pendientes y peraltes.
Se recomienda un cono de trabajo de entre 2 y 5 cms, para el caso de un hormigón vibrado, y entre 5 y 8, en el caso de hormigón apisonado.
Por otra parte, no se colocará hormigón con temperaturas superiores a 35 º C, ni con temperaturas inferiores a 5ºC. En caso contrario, deberán tomarse las precauciones necesarias.

COBERTURA DE HORMIGON EN CONDICIONES EXTREMAS
El hormigón deberá ser esparcido, enrasado y compactado por una o más máquinas para distribuir y compactar el hormigón en forma uniforme, evitando al mínimo las labores manuales.
El hormigón deberá ser esparcido, enrasado y compactado por una o más máquinas para distribuir y compactar el hormigón en forma uniforme, evitando al mínimo las labores manuales.
JUNTAS DE HORMIGONADO.
1. JUNTAS TRANSVERSALES:
DE CONTRACCIÓN.
DE CONSTRUCCIÓN.
DE EXPANSION.
2. JUNTAS LONGITUDINALES:
DE CONSTRUCCIÓN.
DE CONTRACCIÓN.
1.1. JUNTA TRANSVERSAL DE CONTRACCIÓN.
- Su objetivo es inducir en forma ordenada las grietas que se producen a causa de la retracción del hormigón.
- Se recomienda construir a una distancia de 4,5 m entre sí, salvo indicaciones al contrario, debiendo ser perpendiculares o esviadas al eje del camino.
- Salvo que las especificaciones del proyecto indiquen lo contrario, en este tipo de juntas, no se consultan dispositivos de transferencia de cargas.
- En el caso de pavimentos nue
vos contiguos a otros ya existentes, la posición de la nueva junta deberá coincidir con la existente.
DE CONTRACCIÓN.
DE CONSTRUCCIÓN.
DE EXPANSION.
2. JUNTAS LONGITUDINALES:
DE CONSTRUCCIÓN.
DE CONTRACCIÓN.
1.1. JUNTA TRANSVERSAL DE CONTRACCIÓN.
- Su objetivo es inducir en forma ordenada las grietas que se producen a causa de la retracción del hormigón.
- Se recomienda construir a una distancia de 4,5 m entre sí, salvo indicaciones al contrario, debiendo ser perpendiculares o esviadas al eje del camino.
- Salvo que las especificaciones del proyecto indiquen lo contrario, en este tipo de juntas, no se consultan dispositivos de transferencia de cargas.
- En el caso de pavimentos nue

1.1.1. JUNTAS DE CONTRACCIÓN EN EL HORMIGÓN FRESCO.
- Se construye insertando por vibración una pletina en el hormigón fresco.
- El espesor de la pletina es de 4 a 6 mm. Introducida a una altura de 1/3 del espesor del pavimento.
- Una vez retirada la pletina vibradora se introducirá una tablilla no absorbente, generalmente del tipo fibro-cemento o de otro material que no reaccione con el hormigón.
1.1.2. JUNTAS DE CONTRACCION EN EL HORMIGÓN ENDURECIDO.
- Se construye aserrando la superficie del pavimento con un ancho y profundidad indicada por los planos. Se recomienda un espesor de 5 a 8mm y una profundidad igual a 1/3 del espesor del pavimento.
- Se iniciará tan pronto como lo permita el endurecimiento del hormigón.
- Si antes de cortar, se produjeran grietas transversales incontroladas, no se aserrarán las juntas que queden a una distancia menor de 2 metros.

- Se construye insertando por vibración una pletina en el hormigón fresco.
- El espesor de la pletina es de 4 a 6 mm. Introducida a una altura de 1/3 del espesor del pavimento.
- Una vez retirada la pletina vibradora se introducirá una tablilla no absorbente, generalmente del tipo fibro-cemento o de otro material que no reaccione con el hormigón.
1.1.2. JUNTAS DE CONTRACCION EN EL HORMIGÓN ENDURECIDO.
- Se construye aserrando la superficie del pavimento con un ancho y profundidad indicada por los planos. Se recomienda un espesor de 5 a 8mm y una profundidad igual a 1/3 del espesor del pavimento.
- Se iniciará tan pronto como lo permita el endurecimiento del hormigón.
- Si antes de cortar, se produjeran grietas transversales incontroladas, no se aserrarán las juntas que queden a una distancia menor de 2 metros.

Aserrado de una junta de contracción en un hormigón endurecido. Localidad de San Esteban, V Región.
1.2. JUNTAS TRANSVERSALES DE CONSTRUCCIÓN.
1.2. JUNTAS TRANSVERSALES DE CONSTRUCCIÓN.
- Deberán ser construidas cuando hay interrupciones de más de 30 minutos.
- En este tipo de juntas, deben utilizarse dispositivos de transferencia de carga, los cuales serán de acero A-44-28-H (según norma chilena), lisas. Con un largo de 460 mm y ubicadas cada 300 mm.

- En este tipo de juntas, deben utilizarse dispositivos de transferencia de carga, los cuales serán de acero A-44-28-H (según norma chilena), lisas. Con un largo de 460 mm y ubicadas cada 300 mm.

1.3. JUNTAS TRANSVERSALES DE EXPANSION.
- Se usan solamente en determinados casos: empalmes con pavimentos existentes, empalmes con puentes o losas, o en los contornos de cámaras o sumideros.
- Se usan barras de transmisión de cargas de acero A44-28H sin resalte, con un extremo recubierto con betún asfáltico o envainado en PVC.
- La barra de acero deberá estar empotrado en el otro extremo del pavimento, permitiendo su movimiento en completa libertad.
- Se usan solamente en determinados casos: empalmes con pavimentos existentes, empalmes con puentes o losas, o en los contornos de cámaras o sumideros.
- Se usan barras de transmisión de cargas de acero A44-28H sin resalte, con un extremo recubierto con betún asfáltico o envainado en PVC.
- La barra de acero deberá estar empotrado en el otro extremo del pavimento, permitiendo su movimiento en completa libertad.

2.1. JUNTA LONGITUDINAL DE CONSTRUCCION.
- Son aquellas paralelas al eje del camino, a una distancia entre ellas de 3.5 metros, salvo indicaciones del proyecto que indiquen otra distancia.
- Se deberán usar barras de traspaso de cargas ubicadas en el centro del espesor de la losa, dispuestas en posición horizontal. Estas barras serán de acero de calidad (según norma chilena) A-44-28-H con resaltes, de un largo de 650 mm. y de diámetro 12 mm.
- La separación de estas barras será de 650 mm. Estas indicaciones se tomarán en cuenta si el proyecto no indica otra cosa.

- Son aquellas paralelas al eje del camino, a una distancia entre ellas de 3.5 metros, salvo indicaciones del proyecto que indiquen otra distancia.
- Se deberán usar barras de traspaso de cargas ubicadas en el centro del espesor de la losa, dispuestas en posición horizontal. Estas barras serán de acero de calidad (según norma chilena) A-44-28-H con resaltes, de un largo de 650 mm. y de diámetro 12 mm.
- La separación de estas barras será de 650 mm. Estas indicaciones se tomarán en cuenta si el proyecto no indica otra cosa.

2.2. JUNTA LONGITUDINAL DE CONTRACCIÓN.
- Usadas en fajas de pavimento con más de 5 metros de ancho sin juntura longitudinal de construcción.
- Se emplean barras de trabazón de acero con resalte.
- La junta se formará por aserrado con un ancho de 3 a 4 mm y profundidad de 1/3 del espesor del pavimento.
- También puede fabricarse mediante una cinta continua de plástico u otro material que no afecte químicamente el hormigón, a una profundidad mínima de 50mm.
SELLOS DE JUNTAS.
Cuando se especifique el sellado de juntas, éste se hará antes de la entrega al tránsito, usando el material especificado en el Proyecto. Previa a la colocación del sello, la junta debe estar perfectamente limpia y seca.
Deberán respetarse las indicaciones del Proyectista o del Proveedor en cuanto a su forma y tamaño de la junta y condiciones de colocación según el tipo de material.
El material de sellado sólo debe colocarse dentro de la caja de la junta y no sobresalir de la superficie. Todo material de sellos de juntas de pavimento de hormigón, debe cumplir con las siguientes características:
Todo material de sellos de juntas de pavimento de hormigón, debe cumplir con las siguientes características:
Impermeabilidad.
Deformabilidad.
Resiliencia.
Adherencia.
Resistencia.
Estable.
Durable.
En Chile, se ocupan generalmente los sellos de tipo moldeados, los cuales son materiales aplicados en forma líquida o semilíquida, que una vez vaciados en la caja de la junta, forman después de curados, un compuesto de características elásticas. Los hay de dos tipos: termoplásticos y termoestables.
Cuando sea necesario sellar las juntas se aplicará un mastic asfáltico de aplicación en caliente, que cumpla con los requisitos de AASHTO M-173 u otro que se especifique; no se recomienda el empleo de arena o material similar sobre el sello.
El sellado se hará antes de la entrega al tránsito y previa limpieza de la junta con herramientas adecuadas y aire comprimido; el momento de aplicar el material de sello, la junta debe estar seca.
Después del sellado se deberán eliminar los eventuales derrames sobre la superficie.
CURADO Y PROTECCIÓN DEL PAVIMENTO DE HORMIGÓN.
El pavimento deberá curarse aplicando compuestos líquidos que forman una película o membrana impermeable.
Deberán someterse a curado toda la superficie del hormigón expuesto al aire. El periodo de curado será de mínimo seis días, tomando en cuenta las consideraciones establecidas en la norma chilena NCh 170 , anexos D y E.
CARACTERÍSTICAS DE UNA MEMBRANA DE CURADO.
Algunas están formuladas a base de resinas vegetales en dispersión de solventes alifáticos, mientras que otras son de base asfáltica. La aplicación de la membrana se realiza con fumigador sobre el hormigón fresco, no siendo necesario que el pavimento haya perdido el brillo superficial, en el caso del primer tipo de membrana. La formación de la película, a una temperatura promedio de 20º C, se produce entre los 1 a 6 minutos de aplicado el producto. De sus propiedades destacan:
Forman una película instantánea y continua.
Reduce el diferencial térmico del hormigón.
Evita la formación de fisuras superficiales.
Protege al hormigón de agentes climáticos, como temperatura, viento y lluvia.
Aumenta la resistencia mecánica a la abrasión superficial.
De los diversos ensayos que se realizan destacan el de retención de agua, basado en la norma ASTM C 309-81. Según ésta, la pérdida de agua a las 72 horas debe ser como máximo de 0.055 gramos por centímetro cuadrado. Entre las precauciones que se deben tener están:
No aplicar en sobredosis, ya que puede provocar microfisuración de la membrana.
Algunos productos son inflamables.
El equipo de fumigación, debe estar en perfectas condiciones de funcionamiento y limpieza.
RECOMENDACIONES:
Emplear compuestos de curado que cumplan simultáneamente los requisitos de la norma ASTM C 309 y las condiciones siguientes:
Fabricados a base de resinas.
Que reflejen más del 60% de la luz solar.
Que tengan alta viscosidad y sequen al tacto en no más de 30 minutos.
Se puedan colocar inmediatamente después de haber dado textura al pavimento, incluso en presencia de agua superficial.
Seleccionar mediante ensayos a escala natural, el tipo y dosis de la membrana más adecuados para las condiciones de la obra.
Utilizar un rociador mecánico que garantice que el compuesto de curado, quede uniformemente distribuido sobre toda la superficie y costados del pavimento.
Verificar que el compuesto de curado está bien homogeneizado y con el pigmento dispersado uniformemente en el líquido. Durante la aplicación el compuesto se debe agitar continuamente, en lo posible por medio de bombas de recirculación.
Reponer de inmediato la película de curado si se rompe por exudación u otras causas.
Determinar la dosis promedio aplicada, calculando el volumen de compuesto utilizado y la superficie tratada. Cuando se emplean pulverizadores mecánicos, la cantidad colocada por unidad de superficie se controlará mediante el ensayo de la cartulina.
Curar las juntas aserradas. En el caso en que el producto de curado afecte a la adherencia entre la masilla de sellado y el hormigón, las juntas deben protegerse colocando un pabilo de algodón u otro material que las selle provisionalmente, impidiendo la evaporación y la entrada de material extraño.
Emplear techos móviles en zonas de vientos fuertes (sobre 20 km/hr), lluvias y de tormentas intempestivas.
Evitar el tránsito de personas y equipos durante los primeros 7 días. Cuando haya que transitar para aserrar o para controlar la lisura, inmediatamente de terminadas estas operaciones se debe reponer y completar el curado en las zonas en que hubiese resultado dañada la membrana.
CONTROLES Y ENSAYOS.
Durante la ejecución de la faena de hormigonado, deberán practicarse los siguientes ensayos.
Docilidad (según LNV 81).
Densidad y rendimiento (según LNV 87).
Contenido de aire, cuando se usen aditivos incorporadores de aire.
Para comprobar la calidad del hormigón fresco, se efectuaran ensayos de resistencia en probetas prismáticas para ensayos de tracción por flexión, cúbicas para ensayo de compresión, y cilíndrica para ensayos de tracción por hendimiento.
La recepción de la obra, podrá ser en base a testigos que se extraerán según los procedimientos ya establecidos, y los ensayos a realizar serán los de tracción por hendimiento o recepción por compresión. En el primer caso, se tomarán seis probetas gemelas, las que serán ensayadas a la edad de 7 días ( 2 probetas), 28 días ( 2 probetas) y las restantes a 90 días.
En el caso de recepción por compresión, se utilizarán preferentemente probetas cúbicas de 200 mm. de arista. El procedimiento de ensayo es similar al descrito anteriormente.
Además, se controlará el índice de rugosidad internacional ( I.R.I. ), considerando los criterios establecidos en el manual de carreteras, volumen 5 , del ministerio de obras públicas de Chile.
RECOMENDACIONES PARA CONSTRUCCIÓN DE PAVIMENTOS.
El instituto Chileno del cemento y hormigón, entrega una serie de recomendaciones constructivas, destinadas a lograr un mejor rendimiento del pavimento de hormigón. Algunas de ellas son las siguientes:
No usar polietileno en la interfase base-hormigón, ya que no evita el agrietamiento superficial y favorece el alabeo de losas. · Eliminación del rodón central en las juntas del tipo longitudinal.
No colocar barras de amarre contra pistas antiguas.
La apertura al tránsito, se realizará cuando el hormigón alcance , según resistencia a compresión cilíndrica los siguientes valores:
Resistencia mínima de 70 kg/cm2, en el caso que se haya utilizado un hormigón con resistencia de 200 kg/cm2 a las 72 horas.
Resistencia mínima de 150 kg /cm2 en todo otro hormigón.
TIPO DE DEFECTO
CAUSA PROBABLE
PREVENCION Y CORRECCION
Espesor Deficiente
Mala terminación de subbase.
Moldes inadecuados o mal colocados.
Cercha deformada.
Verificar y corregir al recibir canchas previo al hormigonado.
El problema no tiene solución cuando el pavimento está terminado.
Resistencia Insuficiente
Aridos de mala calidad.
Dosificación inadecuada
Exceso de agua de amasado.
Control sistemático y corrección oportuna.
El problema no tiene corrección cuando el hormigón ha endurecido.
Regularidad Superficial
Moldes mal afianzados o desnivelados.
Procedimientos inadecuados; operaciones de terminación defectuosas.
Verificación con regla en el hormigón fresco: rectificación con platacho
Verificación con regla o equipo High-Low en el hormigón recién endurecido: desbastar con disco abrasivo.
Agrietamientos.· En el Hormigón Fresco.
Retracción Plástica:
Dosificación inadecuada.
Agua en exceso.
Viento, aire seco o temperatura ambiente elevada.
Replatachar el hormigón fresco.
En el Hormigón Endurecido.
Retracción de Fraguado:
Curado tardío o inadecuado.
Viento, aire seco o temperatura ambiente elevada.
Exceso de agua.
Dosificación inadecuada.-
Atraso de corte:
Atraso en la ejecución de las juntas cuando éstas se hacen por aserrado.
Mejorar procedimientos de curado.- Fisuras (<>0,5mm):
Impregnación o inyección de resinas antes de puesta en servicio
Modificar procedimientos de confección de juntas.
Dejar las grietas sin tratar para que operen como juntas.
Reparar mediante inyección Epóxica.
- Usadas en fajas de pavimento con más de 5 metros de ancho sin juntura longitudinal de construcción.
- Se emplean barras de trabazón de acero con resalte.
- La junta se formará por aserrado con un ancho de 3 a 4 mm y profundidad de 1/3 del espesor del pavimento.
- También puede fabricarse mediante una cinta continua de plástico u otro material que no afecte químicamente el hormigón, a una profundidad mínima de 50mm.
SELLOS DE JUNTAS.
Cuando se especifique el sellado de juntas, éste se hará antes de la entrega al tránsito, usando el material especificado en el Proyecto. Previa a la colocación del sello, la junta debe estar perfectamente limpia y seca.
Deberán respetarse las indicaciones del Proyectista o del Proveedor en cuanto a su forma y tamaño de la junta y condiciones de colocación según el tipo de material.
El material de sellado sólo debe colocarse dentro de la caja de la junta y no sobresalir de la superficie. Todo material de sellos de juntas de pavimento de hormigón, debe cumplir con las siguientes características:
Todo material de sellos de juntas de pavimento de hormigón, debe cumplir con las siguientes características:
Impermeabilidad.
Deformabilidad.
Resiliencia.
Adherencia.
Resistencia.
Estable.
Durable.
En Chile, se ocupan generalmente los sellos de tipo moldeados, los cuales son materiales aplicados en forma líquida o semilíquida, que una vez vaciados en la caja de la junta, forman después de curados, un compuesto de características elásticas. Los hay de dos tipos: termoplásticos y termoestables.
Cuando sea necesario sellar las juntas se aplicará un mastic asfáltico de aplicación en caliente, que cumpla con los requisitos de AASHTO M-173 u otro que se especifique; no se recomienda el empleo de arena o material similar sobre el sello.
El sellado se hará antes de la entrega al tránsito y previa limpieza de la junta con herramientas adecuadas y aire comprimido; el momento de aplicar el material de sello, la junta debe estar seca.
Después del sellado se deberán eliminar los eventuales derrames sobre la superficie.
CURADO Y PROTECCIÓN DEL PAVIMENTO DE HORMIGÓN.
El pavimento deberá curarse aplicando compuestos líquidos que forman una película o membrana impermeable.
Deberán someterse a curado toda la superficie del hormigón expuesto al aire. El periodo de curado será de mínimo seis días, tomando en cuenta las consideraciones establecidas en la norma chilena NCh 170 , anexos D y E.
CARACTERÍSTICAS DE UNA MEMBRANA DE CURADO.
Algunas están formuladas a base de resinas vegetales en dispersión de solventes alifáticos, mientras que otras son de base asfáltica. La aplicación de la membrana se realiza con fumigador sobre el hormigón fresco, no siendo necesario que el pavimento haya perdido el brillo superficial, en el caso del primer tipo de membrana. La formación de la película, a una temperatura promedio de 20º C, se produce entre los 1 a 6 minutos de aplicado el producto. De sus propiedades destacan:
Forman una película instantánea y continua.
Reduce el diferencial térmico del hormigón.
Evita la formación de fisuras superficiales.
Protege al hormigón de agentes climáticos, como temperatura, viento y lluvia.
Aumenta la resistencia mecánica a la abrasión superficial.
De los diversos ensayos que se realizan destacan el de retención de agua, basado en la norma ASTM C 309-81. Según ésta, la pérdida de agua a las 72 horas debe ser como máximo de 0.055 gramos por centímetro cuadrado. Entre las precauciones que se deben tener están:
No aplicar en sobredosis, ya que puede provocar microfisuración de la membrana.
Algunos productos son inflamables.
El equipo de fumigación, debe estar en perfectas condiciones de funcionamiento y limpieza.
RECOMENDACIONES:
Emplear compuestos de curado que cumplan simultáneamente los requisitos de la norma ASTM C 309 y las condiciones siguientes:
Fabricados a base de resinas.
Que reflejen más del 60% de la luz solar.
Que tengan alta viscosidad y sequen al tacto en no más de 30 minutos.
Se puedan colocar inmediatamente después de haber dado textura al pavimento, incluso en presencia de agua superficial.
Seleccionar mediante ensayos a escala natural, el tipo y dosis de la membrana más adecuados para las condiciones de la obra.
Utilizar un rociador mecánico que garantice que el compuesto de curado, quede uniformemente distribuido sobre toda la superficie y costados del pavimento.
Verificar que el compuesto de curado está bien homogeneizado y con el pigmento dispersado uniformemente en el líquido. Durante la aplicación el compuesto se debe agitar continuamente, en lo posible por medio de bombas de recirculación.
Reponer de inmediato la película de curado si se rompe por exudación u otras causas.
Determinar la dosis promedio aplicada, calculando el volumen de compuesto utilizado y la superficie tratada. Cuando se emplean pulverizadores mecánicos, la cantidad colocada por unidad de superficie se controlará mediante el ensayo de la cartulina.
Curar las juntas aserradas. En el caso en que el producto de curado afecte a la adherencia entre la masilla de sellado y el hormigón, las juntas deben protegerse colocando un pabilo de algodón u otro material que las selle provisionalmente, impidiendo la evaporación y la entrada de material extraño.
Emplear techos móviles en zonas de vientos fuertes (sobre 20 km/hr), lluvias y de tormentas intempestivas.
Evitar el tránsito de personas y equipos durante los primeros 7 días. Cuando haya que transitar para aserrar o para controlar la lisura, inmediatamente de terminadas estas operaciones se debe reponer y completar el curado en las zonas en que hubiese resultado dañada la membrana.
CONTROLES Y ENSAYOS.
Durante la ejecución de la faena de hormigonado, deberán practicarse los siguientes ensayos.
Docilidad (según LNV 81).
Densidad y rendimiento (según LNV 87).
Contenido de aire, cuando se usen aditivos incorporadores de aire.
Para comprobar la calidad del hormigón fresco, se efectuaran ensayos de resistencia en probetas prismáticas para ensayos de tracción por flexión, cúbicas para ensayo de compresión, y cilíndrica para ensayos de tracción por hendimiento.
La recepción de la obra, podrá ser en base a testigos que se extraerán según los procedimientos ya establecidos, y los ensayos a realizar serán los de tracción por hendimiento o recepción por compresión. En el primer caso, se tomarán seis probetas gemelas, las que serán ensayadas a la edad de 7 días ( 2 probetas), 28 días ( 2 probetas) y las restantes a 90 días.
En el caso de recepción por compresión, se utilizarán preferentemente probetas cúbicas de 200 mm. de arista. El procedimiento de ensayo es similar al descrito anteriormente.
Además, se controlará el índice de rugosidad internacional ( I.R.I. ), considerando los criterios establecidos en el manual de carreteras, volumen 5 , del ministerio de obras públicas de Chile.
RECOMENDACIONES PARA CONSTRUCCIÓN DE PAVIMENTOS.
El instituto Chileno del cemento y hormigón, entrega una serie de recomendaciones constructivas, destinadas a lograr un mejor rendimiento del pavimento de hormigón. Algunas de ellas son las siguientes:
No usar polietileno en la interfase base-hormigón, ya que no evita el agrietamiento superficial y favorece el alabeo de losas. · Eliminación del rodón central en las juntas del tipo longitudinal.
No colocar barras de amarre contra pistas antiguas.
La apertura al tránsito, se realizará cuando el hormigón alcance , según resistencia a compresión cilíndrica los siguientes valores:
Resistencia mínima de 70 kg/cm2, en el caso que se haya utilizado un hormigón con resistencia de 200 kg/cm2 a las 72 horas.
Resistencia mínima de 150 kg /cm2 en todo otro hormigón.
TIPO DE DEFECTO
CAUSA PROBABLE
PREVENCION Y CORRECCION
Espesor Deficiente
Mala terminación de subbase.
Moldes inadecuados o mal colocados.
Cercha deformada.
Verificar y corregir al recibir canchas previo al hormigonado.
El problema no tiene solución cuando el pavimento está terminado.
Resistencia Insuficiente
Aridos de mala calidad.
Dosificación inadecuada
Exceso de agua de amasado.
Control sistemático y corrección oportuna.
El problema no tiene corrección cuando el hormigón ha endurecido.
Regularidad Superficial
Moldes mal afianzados o desnivelados.
Procedimientos inadecuados; operaciones de terminación defectuosas.
Verificación con regla en el hormigón fresco: rectificación con platacho
Verificación con regla o equipo High-Low en el hormigón recién endurecido: desbastar con disco abrasivo.
Agrietamientos.· En el Hormigón Fresco.
Retracción Plástica:
Dosificación inadecuada.
Agua en exceso.
Viento, aire seco o temperatura ambiente elevada.
Replatachar el hormigón fresco.
En el Hormigón Endurecido.
Retracción de Fraguado:
Curado tardío o inadecuado.
Viento, aire seco o temperatura ambiente elevada.
Exceso de agua.
Dosificación inadecuada.-
Atraso de corte:
Atraso en la ejecución de las juntas cuando éstas se hacen por aserrado.
Mejorar procedimientos de curado.- Fisuras (<>0,5mm):
Impregnación o inyección de resinas antes de puesta en servicio
Modificar procedimientos de confección de juntas.
Dejar las grietas sin tratar para que operen como juntas.
Reparar mediante inyección Epóxica.
No hay comentarios.:
Publicar un comentario